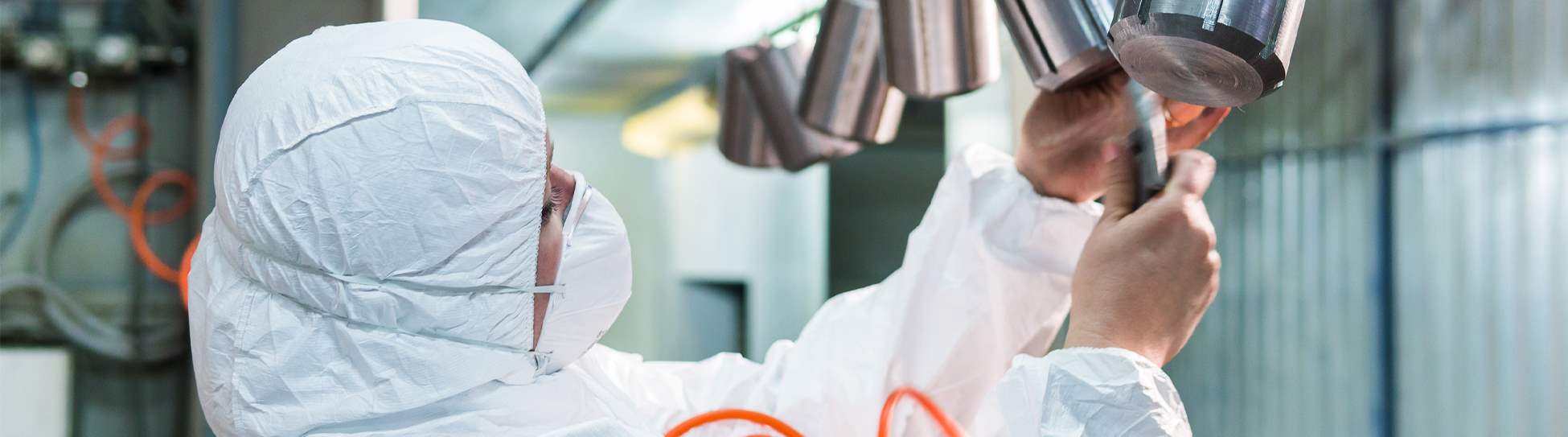
Sand Blast Booth for Pretreatment and Surface Prep
Sanding And Grinding Booths for Blasting Processes
Production Systems is dedicated to supplying sand blasting systems designed and built to meet customer’s specifications. Our reclaim/recovery systems include simple manual recovery to automatic full floor recovery systems. Automatic recovery systems include augers, belt recovery and pneumatic systems. Depending on type of media being used, reclaim can include air wash, cyclones, magnetic separators, vibratory classifiers and heavy particle separators.
Rubber lining of interior walls are available upon request.
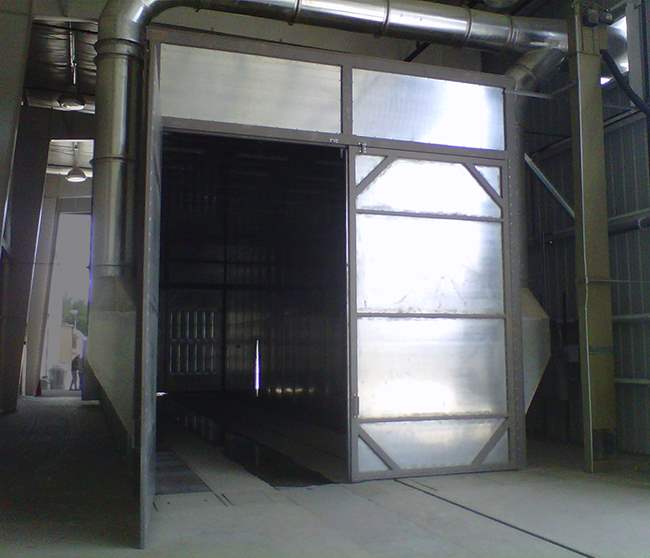
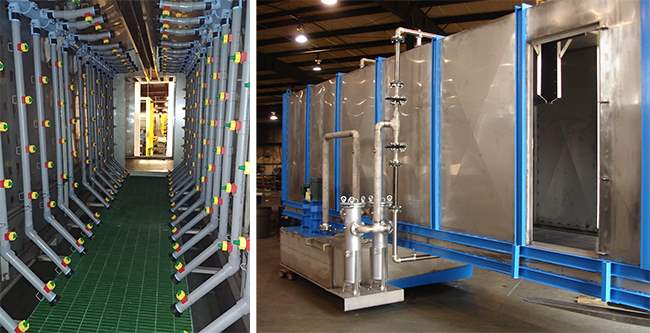
Parts Washers
Parts washers are used for the pre-treatment of parts and components prior to painting. Production Systems will engineer your parts washer with your chemical provider to meet your pretreatment requirements.
Types of Parts Washers
- Non-aqueous single stage plaforization
- Conveyor driven inline power washer
- Multi-stages
- Open top or closed top
TYPICAL PARTS PRE-TREATMENT SPECIFICATIONS
- Washer construction stainless steel, mild steel, other
- Number of stages
- Number of heated stages
- Temperature of each stage
- Process time for each stage
- R/O or DI rinse required
- Package R/O or DI generation system or bottled water system
- R/O or DI holding tank required and capacity
- Sludge doors on tanks
- Misting nozzles between stages
- Insulated tanks on heated stages
- Insulated housing on heated stages
- Electrical controls preference vendor
- Exit end washer blow-off
- Building opening size for washer installation
- Conveyor line speed thru washer
- Max part length in direction of conveyor travel
- Max part size thru washer
- Tank heated by gas, electric, or steam using heat exchanger
- External inline sludge filters (chemical stages only)
- Automatic chemical feed system
- Oil skimmer system
- Type of spray nozzles (hollow cone on conversion stage)
- Open top or closed top design
- Riser centers
- Power voltage
- Stainless steel or CPVC risers
OPEN A DISCUSSION OR SCHEDULE A VISIT
(336) 886-7161